Fugenplatte ist eine Strukturplatte, die durch Zusammenkleben schmalerer Holzbretter (Zuschnitte, Friese) entsteht, die auf die Breite geklebt werden.
Das bekannteste Herstellungsverfahren der Fugenplatte ist die „Stoßverbindung“, ie lediglich durch das Verkleben der gehobelten Kanten zweier Friese entsteht.
Heutzutage wird meist ein moderneres Herstellungsverfahren eingesetzt, nämlich das Fräsen der Flächen mit verschiedenen Profilarten die Kontaktfläche vergrößern.. Dies garantiert eine höhere Festigkeit der Klebeverbindung.
Grundregeln für die Herstellung der Fugenplatte:
Bretter, Latten oder Späne werden immer Kern an Kern und Splintholz an Splintholz verleimt.
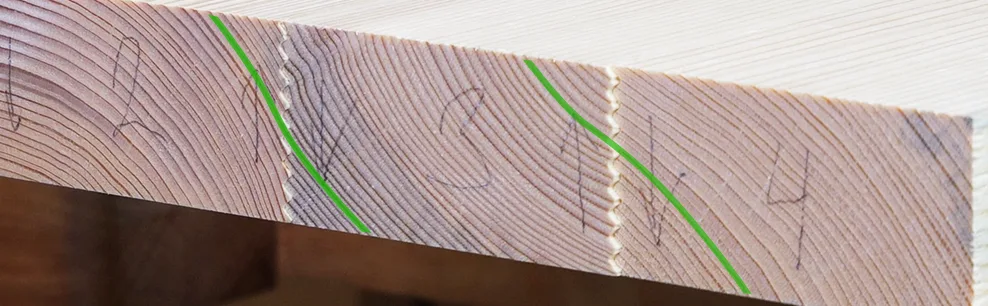
Der mittlere Teil wird nie verwendet.
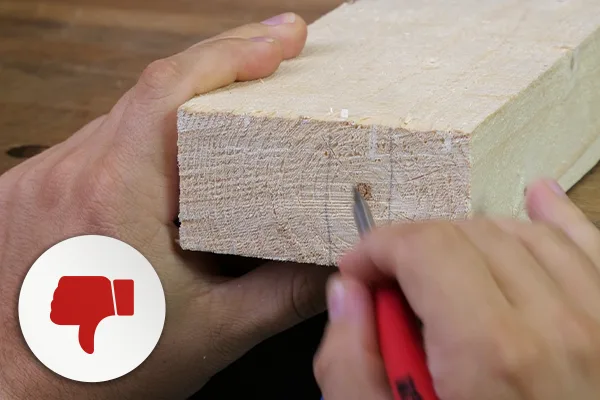
Die Fugenplatte muss aus dem gleichen Holz mit der gleichen Dichte bestehen.
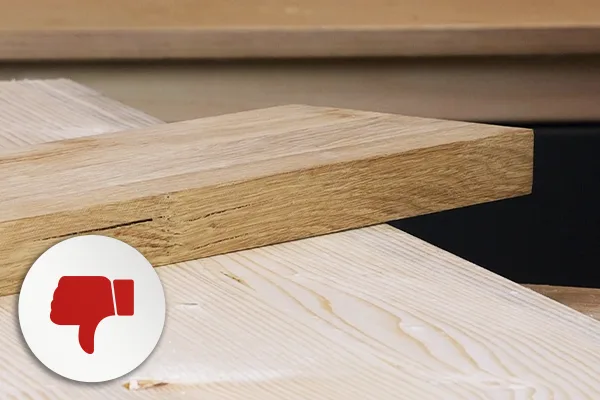
Herstellungsprozess der Fugenplatte Schritt für Schritt
Wir haben uns für ein Verfahren entschieden, bei dem wir mit Profilmessern mit Begrenzern die Oberfläche auf der Unterfräse fräsen, anschließend das Schnittholz verleimen und die Fuge mit einer Dickenhobelfräse spannen.
Ein weiteres mögliches Vorgehen ist auf dem Frästisch mittels Oberfräse und Fräser.
1. Auswahl an Profilmessern
Zunächst müssen Sie ein geeignetes Profilmesser auswählen. Für dieses Verfahren wurde das Profilmesser F026-524 gewählt, das Zähne auf dem Holz erzeugt. Die geriffelte Auflagefläche vergrößert die Leimfläche des Holzes.Diese Verbindung wird dann im Vergleich zu einer „Stumpf“-Verbindung wesentlich stärker sein.
Die Kontaktfläche der Klebefuge kann jedoch auch mit einem anderen Profilmesser gefräst werden. Sie können beispielsweise das Profil 074, 075, 076, 077, 552 oder 117 verwenden.
Da wir auf der Tischfräse ohne Vorschub fräsen werden, verwenden wir zur manuellen Materialzuführung einen Universalfräskopf mit der Bezeichnung MAN Dieser Fräskopf erfordert zusätzlich den Einsatz von Materialbegrenzern. Im Gegensatz zum Profilmesser ist der Begrenzer etwas kürzer und hat keine geschärfte Kante, muss aber immer die gleiche Form haben. In unserem Fall verwenden wir Sicherheits-Abweiser mit der Bezeichnung F027-524.
2. Holzauswahl
Für die Fugenplatte haben wir gehobelte Fichtenbretter mit einer Länge von 1 Meter und einer Dicke von 44 mm verwendet.
Für die Herstellung Ihrer Fugenplatte können Sie jede beliebige Holzgröße wählen.
Für die Herstellung der Fugenplatte müssen Sie lediglich drei Grundregeln beachten: über.
3. Spannen von Profilmessern und Sicherheits-Abweiser
Um die Messer und den Sicherheits-Abweiser richtig in den Fräskopf einzusetzen, legen Sie den Fräskopf so auf den Tisch, dass sich das IGM-Logo auf der Oberseite befindet. Wir platzieren die Profilmesser so im Kopf, dass die Klingen gegen den Uhrzeigersinn zeigen. Die Messer haben zwei kleine runde Löcher, die wir auf die Stifte im Fräskopf stecken müssen.
Anschließend legen wir die Sicherheits-Abweiser in den Fräskopf ein, die wiederum auf die Stifte gesteckt werden. Platzieren Sie den Sicherheits-Abweiser so, dass die Spitze des Sicherheits-Abweisers zur Spitze des Profilmessers zeigt. Sicherheits-Abweiser sind im Uhrzeigersinn gerichtet.
Sobald die Messer und Sicherheits-Abweiser in den Fräskopf eingesetzt sind, halten wir sie mit einer Hand fest und setzen mit der anderen Hand den Spannkeil dazwischen. Die Köpfe der Klemmschrauben im Keil müssen nach außen zeigen.
Wir richten den Keil seitlich am Fräskopfkörper aus und ziehen beide Schrauben mit dem mitgelieferten Inbusschlüssel fest. Ziehen Sie die Schrauben so fest an, dass sich der Keil überhaupt nicht bewegt und die Klingen fest an Ort und Stelle hält.
4. Montage des Fräskopfes an der Tischfräse
Nun können wir den Fräser so auf den Schaft der Tischfräse setzen, dass das IGM-Logo nach oben zeigt. Wir füllen den restlichen Teil des Schafts mit Distanzstücken und ziehen den Fräskopf mit der Spannmutter fest auf dem Schaft fest.
5. Anpassung des Fräskopfes an das Lineal an der Tischfräse
Wir haben das Werkzeug in die Maschine eingebaut. Jetzt müssen wir den Fräskopf und das Längslineal anpassen. Drehen Sie den Fräskopf von Hand bis zum oberen Totpunkt. Der Totpunkt ist die Position des Kopfes, in der die Klinge vom Lineal am weitesten nach außen zeigt, in Richtung des Bedieners der Maschine.
Mithilfe eines Alu-Lineals richten wir das Längslineal exakt auf die größte Profiltiefe unseres Messers aus. Dadurch fräsen wir nur das für die Fuge notwendige Profil und verengen die Friese nicht unnötig durch weiteren Materialabtrag. Das so ausgerichtete Lineal ziehen wir fest an.
6. Berechnung und Einstellung des Fräskopfes
Wir haben den Kopf nach dem Längslineal eingestellt, es bleibt nur noch die Höhe des Fräskopfes einzustellen.
Dazu müssen wir zunächst die genaue Dicke der Friese messen, die wir fräsen werden. In unserem Fall haben wir 44 mm gemessen. Den genauen Mittelpunkt finden wir auf dem Profilmesser. Wenn das Messer 50 mm hoch ist, beträgt der Abstand zur Messerkante 25 mm.
Die halbe Dicke unserer Bretter beträgt 22 mm und die halbe Dicke des Messers beträgt 25 mm. Der Unterschied beträgt also 3 mm. Das bedeutet, dass wir den Fräskopf unter das Tischniveau absenken müssen, sodass die Unterkante des Messers 3 mm unter dem Tischniveau liegt. Die Oberkante des Fräsmessers liegt 47 mm über dem Tisch. Dies können wir mit einem Lineal überprüfen oder mit Hilfe eines Stücks, auf das wir die berechneten 47 mm übertragen.
7. Herstellung einer Kontrollprobe
Nun haben wir das Lineal und die Höhe des Fräskopfes eingestellt und können mit der Arbeit beginnen. Zunächst erstellen wir jedoch ein Testmuster, um die Richtigkeit der Einstellungen zu überprüfen und sicherzustellen, dass die Profile in den Mustern zueinander passen.
Wenn alles in Ordnung ist, können wir uns an die Arbeit machen.
8. Richtige Zusammensetzung und Kennzeichnung des Schnittholzes
Ideal ist es, die Bretter zunächst so zusammenzufügen, wie wir sie verkleben und markieren möchten. Randbretter werden nur von einer Seite gefräst, andere müssen von beiden Seiten gefräst werden. Damit benachbarte Bretter in die Nut des anderen passen und nicht Zahn auf Zahn, muss beim Fräsen jeder zweite Fries um 180° gedreht werden.
Vor dem Fräsen markieren wir alle Bretter auf der Vorderseite, zum Beispiel mit Pfeilen wie auf dem Bild. Oder wir nummerieren die Bretter der Reihe nach. Der Pfeil befindet sich immer nur auf der Vorderseite der Platine und zeigt die Ausrichtung zum Tisch der Fräsmaschine an.
9. Profilfräsen
Beim Fräsen befindet sich der Pfeil immer auf der Seite der Fräsmaschine und muss nach oben zeigen. Befindet sich an der Kante kein Pfeil, ist diese Kante randständig und wird nicht gefräst.
10. Verklebung der Fugenplatte
Anschließend müssen Sie nur noch die gefrästen Kanten mit Holzleim bestreichen. Mit der Titebond-Silikonbürste können wir den Kleber perfekt auch in den gefrästen Rillen verteilen. Zum Verkleben der Fugenplatte eignet sich am besten Titebond Ultimate mit D4-Wasserbeständigkeit. Die Verbindung erhält dann maximale Festigkeit und Haltbarkeit.
Friese mit Kleber müssen mindestens 30 Minuten lang mit Klammern festgeklemmt werden. Die vollständige Aushärtung der Fuge dauert 24 Stunden. Zum Spannen eignen sich die Massive Korpuszwinge IGM, die eine Spannkraft von bis zu 800 kg entwickeln können. Darüber hinaus verhindern die Kunststoffabdeckungen der Backen ein Einbeulen der Friese beim Anziehen.
11. Vergleich der Dicke der Fugenplatte auf der Abricht- und Dickenhobelmaschine
Nach 30 Minuten können wir die Klammern lösen, den überschüssigen Kleber entfernen und die Fugenplatte in einer Dickenhobelmaschine spannen. Wir haben die Verbindung fertig und können daraus beispielsweise eine Sitzbank, eine Tischplatte, einen Türfüller oder alles andere herstellen, was Ihnen zu Hause Freude macht.